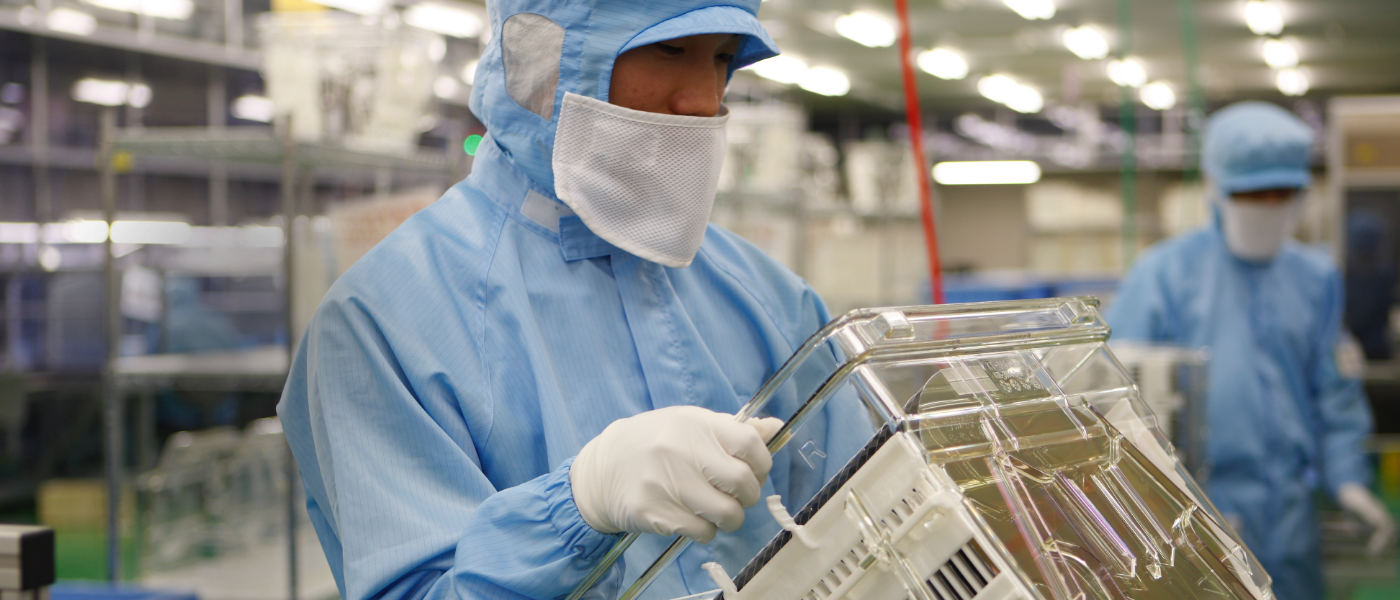
We offer innovative value
through the development of
advanced-function plastic products.
Business Area
Then provide the quality, exactness, and speed required of the customer.
“5 Ms” to achieve Miraial’s Unique value
Molding
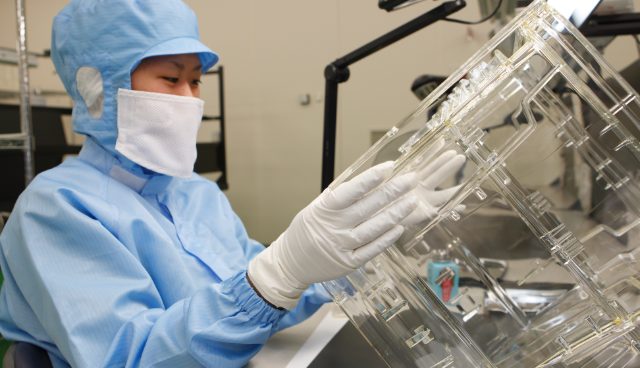
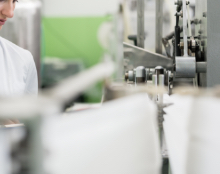
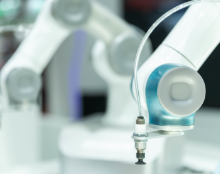
Clean Products, Supporting the Manufacture of Semiconductor Electronic Devices
In the modern age, massive volumes of electronic information are now being handled, and great strides are being made to speed up the processing and communication of that electronic information. The electronic devices used for those purposes are also becoming faster and more precise. This means that silicon wafers, the semiconductor materials used in the manufacturer of electronic devices, must be cleaner than ever. The FOSB, FOUP and other containers that Miraial manufactures play an important role in protecting silicon wafers from the risks of soiling and breakage and keeping them clean during transport. A variety of chemical fluids are also used in the manufacture of semiconductors. Our molded products, made with clean and highly chemical-resistant fluoroplastics, are used in the supply lines for such fluids. In this way, Miraial supports the manufacture of electronic devices by contributing to the clean manufacture of semiconductors.
Large Precision Molding
With equipment ranging from small injection molding machines with a clamping force of 30 tonnes to large 3,000-tonne injection molding machines, Miraial can accommodate products of varying sizes, from just a few square millimeters to 500 square millimeters. Injection molding involves pouring molten plastic into a mold and cooling it down to make products, making it an excellent processing method for mass production of the same product in a short cycle. On the other hand, it is susceptible to deformation, such as fluctuations in dimensions and warping, the effects of which are particularly noticeable in large items.
Taking advantage of the injection molding technologies that we have cultivated over many years, Miraial controls the molding conditions with minute precision to reduce dimension changes and deformation, enabling us to product large, precision-molded items.
Leveraging Super Engineering Plastics’ Properties to Change the Norms
Super engineering plastics have excellent heat and chemical resistance, but their poor molding process-ability (fluidity) and large shrinkage factor make it difficult to control dimensions and external appearance. For this reason, they are harder to mold than general-purpose plastics. At Miraial, leveraging the injection molding technologies we have cultivated over many years, we have succeeded in using super engineering plastics to deliver products with more advanced functions to the market. These products, which take advantage of super engineering plastics’ properties, including their heat resistance, chemical resistance, and non-adhesiveness, are used in many different sectors, including semiconductors, medical and pharmaceutical, chemicals, and food products. Other products we are involved in include relay terminals for electronic devices, using compression molding and machining, and fluid bottles, using blow molding.

Machinery
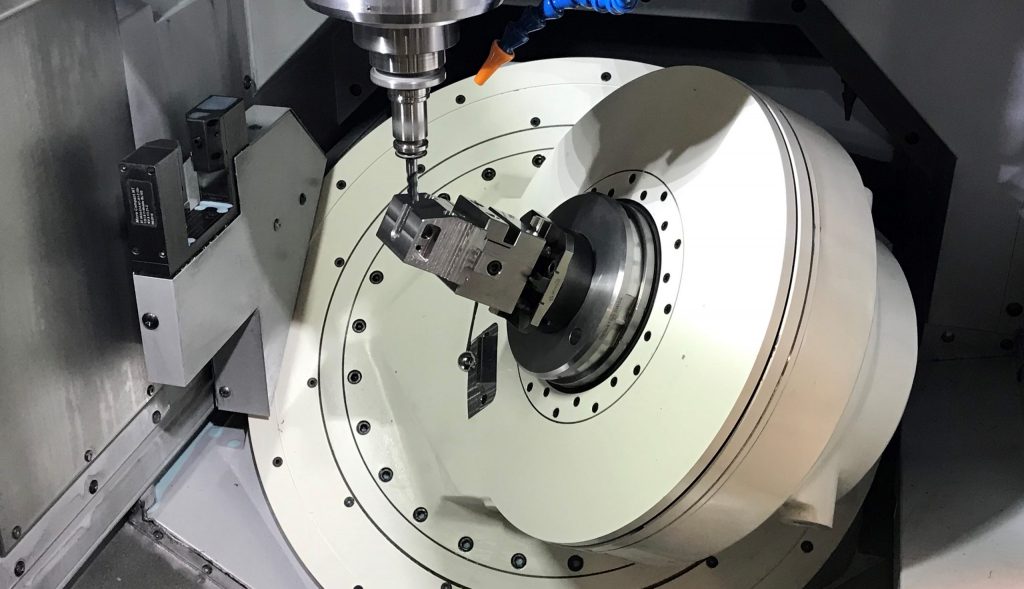
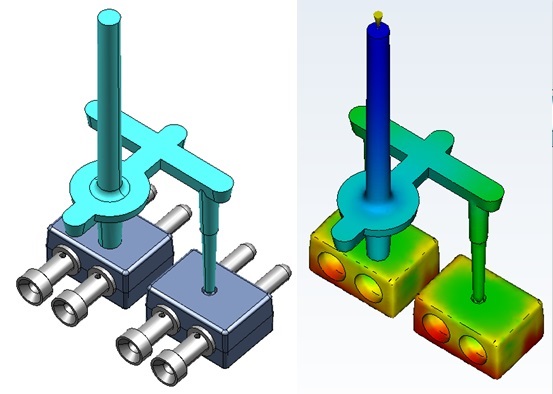
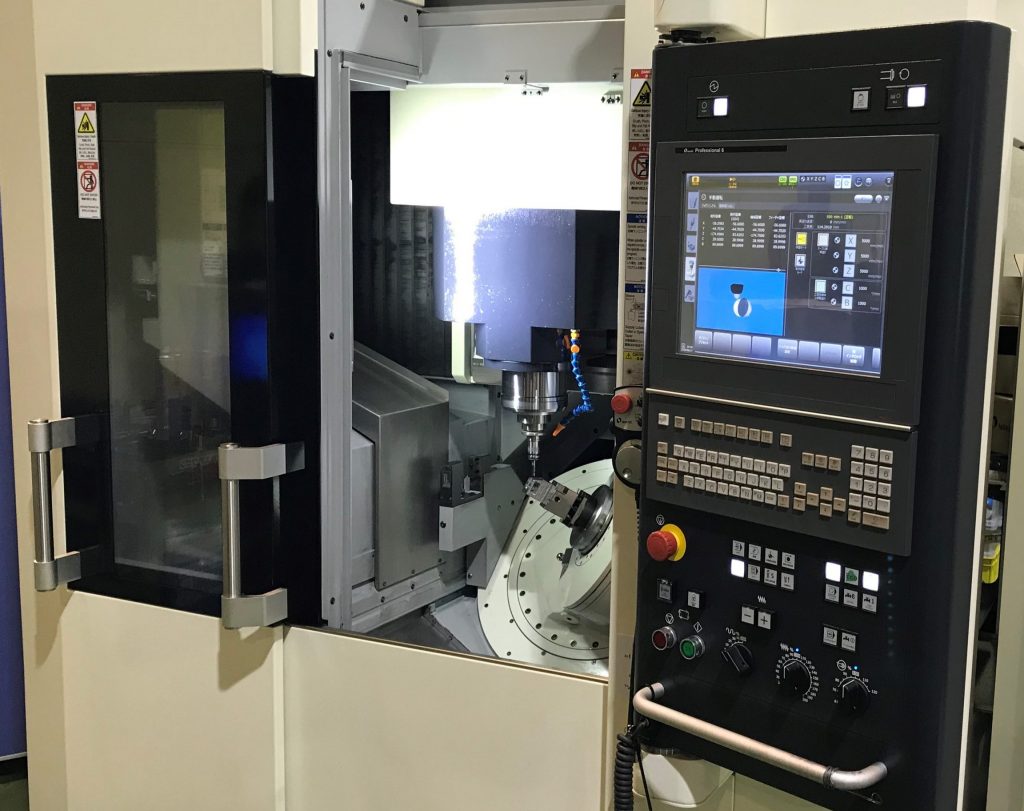
Molding Machines and Automation Devices
Plastic molding machines require three functions: (1) melt the molding material; (2) pour the molten material into the mold, and (3) set the material in the mold to create a shape.
Approximately 90% of the plastic molding machines manufactured around the world have a horizontal layout, with the injection mechanism that melts and pours the material and the clamping mechanism that closes the mold positioned side by side. However, we have adopted a vertical layout for our machines and have continued to manufacture molded items as a pioneer in vertical molding machines.
Vertical molding machines are particularly suited to insert molding, in which metal components and other components are inserted into the plastic and molded together, because the insert can be held stable inside the mold without defying gravity. Also, because the molded items produced from the poured and set resin stay in place even after the mold is opened, they can be removed from the mold in a stable condition.
Taking advantage of these characteristics, we accommodate the composite molding of insert components of all manner of materials and structures and vastly diverse molding materials, offering molding machines to meet the needs of our customers. Our watchword is our willingness to respond to even the smallest request.
In addition to molding machines and metal molds, we develop and produce peripheral automation devices, control devices, and various types of testing devices.
Leveraging these comprehensive technological capabilities, we deliver integrated systems, including software, on a turnkey basis.
Metal Molds
Our metal molds accommodate a wide range of molding materials, including thermoplastic resins (from general-purpose to super engineering plastics), thermosetting resins (epoxy, BMC, phenols), silicon rubber, ceramic, fluoroplastics, and CFRP, and different inserts, including motor parts, electronic substrates, various types of hoop, ISO test blocks, and color plates. We also offer cartridge molds that are most suited to molding of a wide variety of products in small quantities.
We will make the best proposals regarding material and surface treatment for your application, including molding material, insert, prototype, and mass production.
For production of the mold, we carry out a series of operations from design using 3D data to flow analysis and machining program, machining the mold speedily to a high standard, predominantly with our state-of-the-art 5-axis machining center. We measure the mold parts using image measurement and 3D measurement devices in the pursuit of quality at the individual part level.
After assembly and adjustment of the mold, we produce a prototype using the optimal equipment for the material from our range of in-house molding equipment suited to various material types.
The molded prototype immediately undergoes various measurements, based on which the mold will be corrected as necessary to provide the customer with satisfactory product.

Modeling & machining
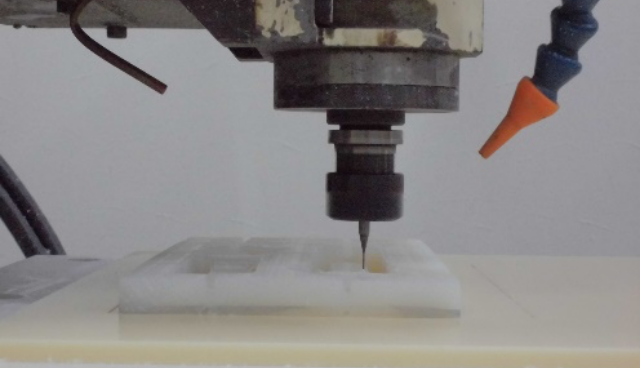
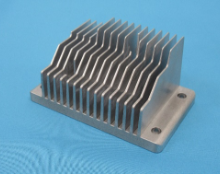
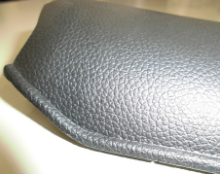
Machining - A Process of Subtraction
Machining is a process in which machine tools are used to cut out the shape of a product from a raw member such as a plate or rod.
We are able to work with a wide range of materials, including many types of resin from general-purpose to super engineering plastics, and a variety of metals, including aluminum and stainless steel. We are even able to work with metals that are difficult to cut, such as titanium and nickel alloys.
The equipment we use for machining includes a machining center and NC compound lathes, which use numerical control to perform machining automatically with a high degree of complexity and precision. Our systems allow us to use multiple types of tool to cut a piece from many directions in a single program, or to machine multiple products from multiple pieces laid out on the machining table, all in an automated process, greatly reducing machining times.
Our high degree of responsiveness and precision are put to use in the fabrication of diverse products and various types of jig. We are also able to perform additional machining of molded items.
3D-Printing and Casting - Processes of Addition
3D-printing is a process in which materials are added and built up to create the shape of a product.
Using the minimal quantity of material necessary, 3D-printing can produce complex shapes that are difficult to achieve with machining.
For plastic reproduction of the same shape in quantities ranging from a handful to several dozen, we recommend vacuum casting. This technology, which is used to make plastic reproductions, involves making a silicon mold from a master model made by 3D-printing or machining, then pouring a urethane resin into that mold in a vacuum chamber. Surface treatment for textured or glossy surfaces, insertion of metal components, and integrated casting with different resins are also possible with this method. Vacuum casting can offer plastic products with a shorter turnaround and at a lower price than metal molds.

Material
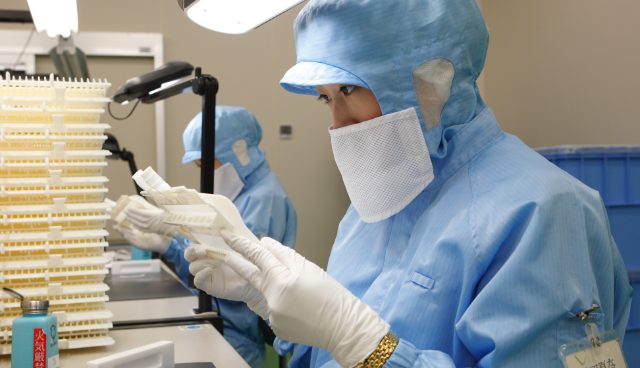
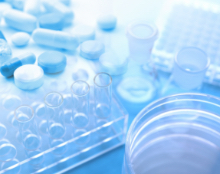
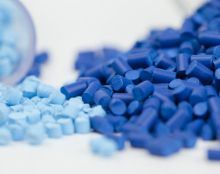
Analysis - Knowing the Material
The functions of a product are greatly influenced by the material used, so when developing a product to satisfy the customer’s requirements, it is important to select the right material for that product. To do this, we must first analyze the material and understand its functions and properties. At Miraial, we use a variety of analytical equipment to analyze the physical properties of materials, such as mechanical strength, wear resistance, and heat resistance. This allows us to understand the functions and properties that are peculiar to the material and make use of that information in product design. Our day-to-day efforts in this area are important so we can develop better products.
Enhancing Functions with Conjugations of Materials
By combining single resin materials and compounding it with materials that have a variety of functions, we can give the resin functions that a single material by itself does not possess, such as heat resistance, electric conductivity, and greater strength. Those functions can be diversified depending on the combination of materials, making the possibilities endless. Because Miraial is able to compound materials in-house, we can develop resins that are not available on the market by compounding resin materials into advanced-function materials. Our aim is to use those materials to develop products with more advanced functions.

Metrology
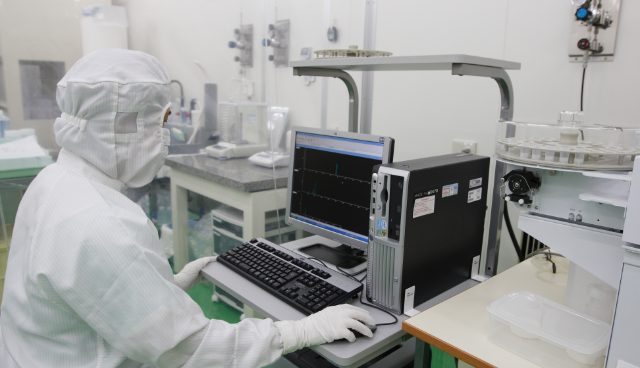
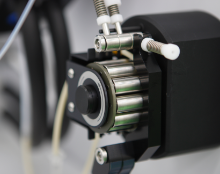
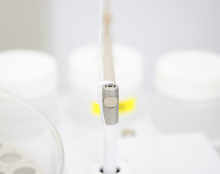
Chemical Analysis - Supporting Product Quality with Cleanliness Controls
As semiconductors have become increasingly miniaturized, the cleanliness requirements for products have also increased. To meet those requirements, Miraial measures the cleanliness (ions, metals, outgas) of raw materials and finished products in the order of ppt, controlling cleanliness with statistical methods. By continuously improving our processes based on the results of those measurements, we strive to maintain frameworks for the stable supply of clean products.
